Siden Systemair begynte med serienummersystem i 2006, kunne de 18. desember i fjor feire at aggregat nr. 10.000 rullet ut dørene fra fabrikken på Dal i Eidsvoll. Selskapet har hatt stor suksess med sine kortreiste, energieffektive og norskproduserte ventilasjonsaggregater, som er levert til alle typer bygg over hele landet.
VVS Forum slo av en prat med markedssjef Amund Ona Gjul om hva som ligger bak suksesshistorien på Dal, og hvordan veien videre ser ut for Systemair i Norge.
Hva er bakgrunnen for suksessen?
- Historien til Systemair på Eidsvoll strekker seg langt tilbake, med riktig fokus, smarte beslutninger og god forretningsdrift over flere tiår. Vi har tatt frem gode, konkurransedyktige produkter som markedet etterspør, og vi har turt å pushe utviklingen i riktig retning med introduksjon av stadig mer energigjerrige komponenter og løsninger.
Han forteller videre at det å gjøre ting enkelt og effektivt for kunden alltid har vært høyt prioritert.
- Store ressurser er lagt ned i pålitelig logistikk og et godt supportapparat. Vi så også tidlig behovet for gode, digitale verktøy for planlegging og prosjektering. Her satte vi standarden med SystemairCAD, som fremdeles er det foretrukne aggregatberegningsprogrammet for de fleste konsulenter, sier han.
- Skal jeg peke på det viktigste suksesskriteriet til Systemair, må det være selskapets evne til å holde på de gode folkene - alle de som jobbet i produksjonen i 2006 er fremdeles med oss.
Hvilke utfordringer følger med industriell produksjon i Norge?
- Vi har et generelt høyt kostnadsnivå i Norge. Vi nordmenn er også tilsynelatende glade i regelverk, saksbehandling og papirarbeid. Når utbyggingsplaner og investeringsvilje i varige norske arbeidsplasser blir stagget av 4 grantrær på et regulert industriområde, er det på tide å stikke fingeren i jorda. Vi er også smertelig klar over at dersom kundene våre kunne spart noen tusenlapper på å handle utenlandsk, ville de gjort det. Til tross for dette viser vi at norsk aggregatproduksjon er konkurransedyktig sier han, og tilføyer:
- Med vår fabrikk på Eidsvoll har vi en nærhet til markedet som lønner seg. Transport på trailer fra kontinentet koster - både økonomisk og miljømessig. Med lokal produksjon følger også viktig, lokal kompetanse. Jeg tror det ligger en verdi for våre kunder å få hjelp på godt romeriksmål, uansett om det gjelder logistikk eller teknikk, avslutter han.
Hvordan har produksjonen utviklet seg over årene?
- Med nye, mer avanserte produkter følger nye, mer avanserte produksjonsmetoder. Vi har investert rundt 30 millioner kroner de siste årene i fabrikken vår på Eidsvoll, med ny robotisert produksjonslinje og nye lagerfasiliteter. Med dette legger vi forholdene til rette for fortsatt konkurransekraft og videre vekst, sier han.
- Vår nye aggregatserie Geniox, krever mer bearbeidelse av tynnplatestålet. Dette tunge, gjentagende arbeidet tar nå robotene seg av, og vi kan bruke de menneskelige ressursene mer fornuftig, blant annet i sluttmontasjen. Driften vår har gjennomgått en betydelig modernisering de siste årene. Dette gir økt konkurransekraft, og automatiseringen har ført til flere arbeidsplasser - ikke færre, konstaterer Gjul.
I bildet til venstre ser vi aggregatet Geniox som er selskapet nye ventilasjonsaggregat, mens man til høyre ser automatiserte produksjonssystemer fra fabrikken på Dal.[/caption]
Hvordan fokuserer dere på fremtidens energieffektive løsninger?
- Selskapet legger ned mye ressurser i produktutvikling, med små og store produktforbedringer for bedre ytelse, redusert energibruk og mindre miljøbelastning. Våre produkter har en levetid på flere tiår, og det er i driftsfasen de har sitt bidrag. Vårt fokus er derfor å lage robuste produkter tilrettelagt for energioptimal regulering og drift, og rustet for et langt og energigjerrig liv i norsk bygningsmasse, sier Gjul.
Han ser med bekymring på en del trender i bransjen, der fokuset blir forsøkt endret til marginale problemstillinger:
- Den dagen mengden emballasje, isolasjon eller stål blir avgjørende for valg av ventilasjonsaggregat, blir en sørgelig dag for både miljø, bransje, byggherre og sluttbruker. CO2-utslippet forbundet med stålproduksjonen til et ventilasjonsaggregat er kompensert for ved å redusere SFP-faktoren med beskjedne 1-1,5 %. For alle som mener alvor bør det ikke være tvil om hvor fokuset bør være, mener Gjul.
- Som bransje må vi vokte oss. Tunnelsynet kommer krypende, det samme gjør fordyrende sertifiseringsordninger og tilhørende konsulentjobber som skal regulere, beregne, dokumentere og revidere. Alt må betales for, og pengene kan kun brukes én gang. Hvilke slagkraftige, økonomisk lønnsomme energieffektiviseringstiltak må prioriteres bort i et slikt marked, spør han.
- I Systemair jobber vi bredt med bærekraft, og er vårt ansvar bevisst. Vi bruker rundt 450 000 arbeidstimer i året på produktutvikling, i søken etter stadig smartere og mer energieffektive løsninger. Jeg håper inderlig at vi ikke må flytte ressurser over på kostnadsdrivende, dødt papirarbeid og «grønne gimmicker», avslutter han.
Hvordan tror du fremtidens produkter og løsninger ser ut?
- Folk trenger frisk luft å puste i, og mekanisk, balansert ventilasjon med varmegjenvinning er den mest energi- og kostnadseffektive måten å tilfredsstille dette behovet på. Hybride løsninger vil vi nok se mer av i årene som kommer, mener Gjul.
Fra fabrikken på Eidsvoll har selskapet levert aggregater til de mest ambisiøse byggene i landet, blant annet Powerhouse-prosjektene.
I Powerhouse Brattørkaia står aggregatene for hele klimatiseringen, med både kjøling og oppvarming via ventilasjonsluften. I takt med stadig lavere oppvarmingsbehov vil nok slike løsninger bli mer utbredt, forteller han
Ventilasjonsanleggene på Powerhouse Brattørkaia vises frem på ZEB+ konferansen.[/caption]
I november deltok selskapet på ZEB+ konferansen i Trondheim, der Powerhouse Brattørkaia var tema.
På konferansen ble også et annet miljømessig prestisjeprosjekt omtalt. Bygget hadde vært i drift et års tid, men på grunn av en driftsfeil hadde ventilasjonsaggregatet gått 24 timer i døgnet på full luftmengde, uten at det ble oppdaget. Som et resultat ble energibruken høyere enn for et tradisjonelt bygg og presentasjonen ble noe amputert. Men lærdommen fra slike feil er likevel viktig, sier han og fortsetter:
- Å sikre energioptimal drift er vår viktigste oppgave. Dette begynner med utvelgelsen av riktig aggregat med riktig kapasitet, tilpasset bygget og tilsiktet bruk. Videre handler det om robuste og brukervennlige løsninger som gjør det enkelt å få aggregatet riktig montert og konfigurert i teknisk rom. Fremtidsrettet elektronikk og automatikk som muliggjør optimal regulering og full kontroll, uansett hvor man sitter hen, blir også avgjørende. I takt med økende out-sourcing av drift og vedlikehold blir det stadig viktigere å minimere feil, sikre enkelt og effektivt vedlikehold og påse at eventuelle avvik lar seg identifisere og utbedre raskest mulig, sier Gjul.
Etter hvert som digitaliseringen gjør sitt inntog vil det nok merkes, også i ventilasjonsbransjen. Smarte sensorer, i kombinasjon med store databaser med driftsdata, vil på sikt gi oss løsninger for prediktivt vedlikehold. Man venter ikke til noe har gått galt, men får beskjed noen uker i forveien at noe må skiftes. På den måten kan ettersyn og vedlikehold optimaliseres, og man slipper kostbare driftsstanser, sier han.
Vi er godt rustet for å møte både utfordringene og mulighetene fremtiden byr på. Vi har en topp moderne produksjon, et helt nytt aggregat under oppseiling, og ikke minst et knallgodt team. Energioptimal klimatisering er i vinden, og vi er klare til å bidra, avslutter Gjul.
VVS Forum slo av en prat med markedssjef Amund Ona Gjul om hva som ligger bak suksesshistorien på Dal, og hvordan veien videre ser ut for Systemair i Norge.
Hva er bakgrunnen for suksessen?
- Historien til Systemair på Eidsvoll strekker seg langt tilbake, med riktig fokus, smarte beslutninger og god forretningsdrift over flere tiår. Vi har tatt frem gode, konkurransedyktige produkter som markedet etterspør, og vi har turt å pushe utviklingen i riktig retning med introduksjon av stadig mer energigjerrige komponenter og løsninger.
Han forteller videre at det å gjøre ting enkelt og effektivt for kunden alltid har vært høyt prioritert.
- Store ressurser er lagt ned i pålitelig logistikk og et godt supportapparat. Vi så også tidlig behovet for gode, digitale verktøy for planlegging og prosjektering. Her satte vi standarden med SystemairCAD, som fremdeles er det foretrukne aggregatberegningsprogrammet for de fleste konsulenter, sier han.
- Skal jeg peke på det viktigste suksesskriteriet til Systemair, må det være selskapets evne til å holde på de gode folkene - alle de som jobbet i produksjonen i 2006 er fremdeles med oss.
Hvilke utfordringer følger med industriell produksjon i Norge?
- Vi har et generelt høyt kostnadsnivå i Norge. Vi nordmenn er også tilsynelatende glade i regelverk, saksbehandling og papirarbeid. Når utbyggingsplaner og investeringsvilje i varige norske arbeidsplasser blir stagget av 4 grantrær på et regulert industriområde, er det på tide å stikke fingeren i jorda. Vi er også smertelig klar over at dersom kundene våre kunne spart noen tusenlapper på å handle utenlandsk, ville de gjort det. Til tross for dette viser vi at norsk aggregatproduksjon er konkurransedyktig sier han, og tilføyer:
- Med vår fabrikk på Eidsvoll har vi en nærhet til markedet som lønner seg. Transport på trailer fra kontinentet koster - både økonomisk og miljømessig. Med lokal produksjon følger også viktig, lokal kompetanse. Jeg tror det ligger en verdi for våre kunder å få hjelp på godt romeriksmål, uansett om det gjelder logistikk eller teknikk, avslutter han.
Hvordan har produksjonen utviklet seg over årene?
- Med nye, mer avanserte produkter følger nye, mer avanserte produksjonsmetoder. Vi har investert rundt 30 millioner kroner de siste årene i fabrikken vår på Eidsvoll, med ny robotisert produksjonslinje og nye lagerfasiliteter. Med dette legger vi forholdene til rette for fortsatt konkurransekraft og videre vekst, sier han.
- Vår nye aggregatserie Geniox, krever mer bearbeidelse av tynnplatestålet. Dette tunge, gjentagende arbeidet tar nå robotene seg av, og vi kan bruke de menneskelige ressursene mer fornuftig, blant annet i sluttmontasjen. Driften vår har gjennomgått en betydelig modernisering de siste årene. Dette gir økt konkurransekraft, og automatiseringen har ført til flere arbeidsplasser - ikke færre, konstaterer Gjul.
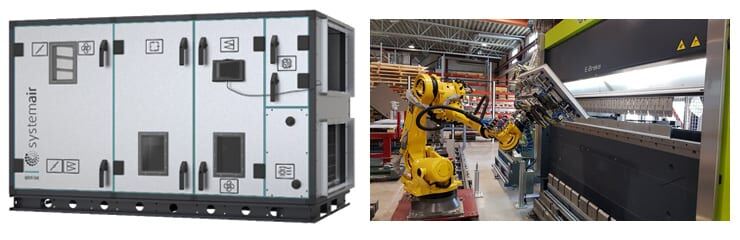
Hvordan fokuserer dere på fremtidens energieffektive løsninger?
- Selskapet legger ned mye ressurser i produktutvikling, med små og store produktforbedringer for bedre ytelse, redusert energibruk og mindre miljøbelastning. Våre produkter har en levetid på flere tiår, og det er i driftsfasen de har sitt bidrag. Vårt fokus er derfor å lage robuste produkter tilrettelagt for energioptimal regulering og drift, og rustet for et langt og energigjerrig liv i norsk bygningsmasse, sier Gjul.
Han ser med bekymring på en del trender i bransjen, der fokuset blir forsøkt endret til marginale problemstillinger:
- Den dagen mengden emballasje, isolasjon eller stål blir avgjørende for valg av ventilasjonsaggregat, blir en sørgelig dag for både miljø, bransje, byggherre og sluttbruker. CO2-utslippet forbundet med stålproduksjonen til et ventilasjonsaggregat er kompensert for ved å redusere SFP-faktoren med beskjedne 1-1,5 %. For alle som mener alvor bør det ikke være tvil om hvor fokuset bør være, mener Gjul.
- Som bransje må vi vokte oss. Tunnelsynet kommer krypende, det samme gjør fordyrende sertifiseringsordninger og tilhørende konsulentjobber som skal regulere, beregne, dokumentere og revidere. Alt må betales for, og pengene kan kun brukes én gang. Hvilke slagkraftige, økonomisk lønnsomme energieffektiviseringstiltak må prioriteres bort i et slikt marked, spør han.
- I Systemair jobber vi bredt med bærekraft, og er vårt ansvar bevisst. Vi bruker rundt 450 000 arbeidstimer i året på produktutvikling, i søken etter stadig smartere og mer energieffektive løsninger. Jeg håper inderlig at vi ikke må flytte ressurser over på kostnadsdrivende, dødt papirarbeid og «grønne gimmicker», avslutter han.
Hvordan tror du fremtidens produkter og løsninger ser ut?
- Folk trenger frisk luft å puste i, og mekanisk, balansert ventilasjon med varmegjenvinning er den mest energi- og kostnadseffektive måten å tilfredsstille dette behovet på. Hybride løsninger vil vi nok se mer av i årene som kommer, mener Gjul.
Fra fabrikken på Eidsvoll har selskapet levert aggregater til de mest ambisiøse byggene i landet, blant annet Powerhouse-prosjektene.
I Powerhouse Brattørkaia står aggregatene for hele klimatiseringen, med både kjøling og oppvarming via ventilasjonsluften. I takt med stadig lavere oppvarmingsbehov vil nok slike løsninger bli mer utbredt, forteller han
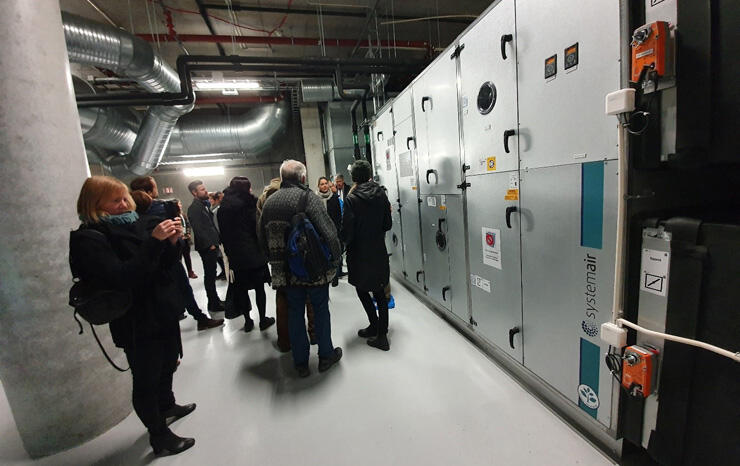
I november deltok selskapet på ZEB+ konferansen i Trondheim, der Powerhouse Brattørkaia var tema.
På konferansen ble også et annet miljømessig prestisjeprosjekt omtalt. Bygget hadde vært i drift et års tid, men på grunn av en driftsfeil hadde ventilasjonsaggregatet gått 24 timer i døgnet på full luftmengde, uten at det ble oppdaget. Som et resultat ble energibruken høyere enn for et tradisjonelt bygg og presentasjonen ble noe amputert. Men lærdommen fra slike feil er likevel viktig, sier han og fortsetter:
- Å sikre energioptimal drift er vår viktigste oppgave. Dette begynner med utvelgelsen av riktig aggregat med riktig kapasitet, tilpasset bygget og tilsiktet bruk. Videre handler det om robuste og brukervennlige løsninger som gjør det enkelt å få aggregatet riktig montert og konfigurert i teknisk rom. Fremtidsrettet elektronikk og automatikk som muliggjør optimal regulering og full kontroll, uansett hvor man sitter hen, blir også avgjørende. I takt med økende out-sourcing av drift og vedlikehold blir det stadig viktigere å minimere feil, sikre enkelt og effektivt vedlikehold og påse at eventuelle avvik lar seg identifisere og utbedre raskest mulig, sier Gjul.
Etter hvert som digitaliseringen gjør sitt inntog vil det nok merkes, også i ventilasjonsbransjen. Smarte sensorer, i kombinasjon med store databaser med driftsdata, vil på sikt gi oss løsninger for prediktivt vedlikehold. Man venter ikke til noe har gått galt, men får beskjed noen uker i forveien at noe må skiftes. På den måten kan ettersyn og vedlikehold optimaliseres, og man slipper kostbare driftsstanser, sier han.
Vi er godt rustet for å møte både utfordringene og mulighetene fremtiden byr på. Vi har en topp moderne produksjon, et helt nytt aggregat under oppseiling, og ikke minst et knallgodt team. Energioptimal klimatisering er i vinden, og vi er klare til å bidra, avslutter Gjul.